Computer numerical control (CNC) machining, leverages automation to produce components faster and more accurately than manual labor affords. Thanks to their efficiency and precision, CNC machining methods have become standard for moderate to high-volume production across industries.
CNC turning, in particular, simplifies the process of creating small and intricate cylindrical components such as precisely-threaded screws, nuts, and fittings. Precision turning techniques like Swiss machining yield components as diverse as watch collets, medical implants, and firearm barrels, all with high-throughput and minimal secondary processing.
As experts in precision turning, DACRUZ Manufacturing employs Swiss machining technology to produce intricate components with back-machined and cross-machined features. Our Swiss centers are complemented by bar-fed CNC lathes for larger jobs and a full suite of secondary services for complex components. Together, these capabilities allow us to serve OEMs with diverse machining needs.
Swiss CNC Machining
Swiss machining is a type of CNC turning used to create highly precise components, especially those with slender profiles and fine details. Swiss CNC machines can be described as advanced, automated lathes with extra tooling stations. However, Swiss centers have several features that distinguish them from conventional lathes. These features, which include a moving headstock and multi-axis capabilities, enable the superior precision that differentiates Swiss machining from other methods.
How Does Swiss Machining Work?
In most CNC turning stations, the part rotates within a fixed headstock while the cutting tools move back and forth to shape the component. Swiss stations use a moving headstock to advance the workpiece to the tools, along with a guide bushing to support the bar as it is formed. The workpiece progresses through a guide bushing as it rotates so that only part of the component is exposed at a given time increasing stability and precision. As the piece rotates, tools cut within millimeters of the guide bushing, eliminating most deflection and maintaining extremely tight tolerances.
Another key difference is that Swiss machining centers feature more axes of motion and perform more operations simultaneously. Depending on the station, Swiss machines can have more than 10 machining axes, compared to the traditional 3-4. With these additional axes and tools, Swiss machines can turn, mill, and thread all in the same cycle. Combining multiple processes in this way enables net-shape manufacturing, which increases both efficiency and repeatability.
Together, these characteristics dramatically reduce cycle times and minimize the need for secondary processing. As a result, Swiss machines can output small and precise components much faster than conventional methods.
Benefits of Swiss CNC Machining
Swiss machining centers are valuable because they enable high-volume, high-precision production of varied components. Notable benefits of Swiss CNC machining include:
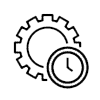
Productivity
Conventional lathes are limited to performing operations in sequence, so complex components require multiple, time-consuming cycles. By contrast, Swiss centers perform several processes simultaneously, including operations that would traditionally require secondary processing. These benefits result in significantly shorter cycle times and enhanced productivity overall.
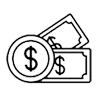
Cost Savings
Swiss machines reduce manufacturing costs, generating savings that pass onto clients. These savings come from two primary sources: First, since Swiss centers are so much more efficient, they allow the same component to be produced faster and with fewer labor costs. Second, the precision of Swiss machining allows manufacturers to use smaller bar stock, reducing both material costs and waste. Finally, in addition to reducing manufacturing costs, Swiss machining also reduces development costs by eliminating the need for custom tooling.
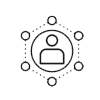
Versatility
Swiss machining’s versatility underlies many of its other benefits. Swiss CNC centers can hold over 20 tools and accomplish both turning and milling processes simultaneously. These machines can also handle a wide range of metals and can be used to create parts ranging from 10 mm to 32 mm in diameter.
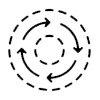
Consistency
Reducing or eliminating secondary processing lessens variability in the manufacturing process for maximum repeatability. Clients benefit from single-process machining via more consistent product batches with tighter tolerances and fewer defects.
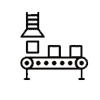
Increased Production Volumes
Swiss lathes can be run unmanned, which not only reduces labor costs but also enables greater product output. Lights out machining, in which manufacturing proceeds outside of normal business hours, is ideal for this purpose.
Overall, Swiss CNC machining is the best option for clients seeking rapid, cost-effective production of precision-turned components.
Swiss CNC Machining Applications and Industries
- Aerospace: Aerospace components come with some of the tightest tolerance requirements across industries. Swiss machining makes it easy to meet these stringent specifications, even for intricate components. Pressnuts, screws, shafts, and similar parts can all be crafted from performance alloys with unsurpassed precision.
- Automotive: Automotive components have similar, though less rigorous constraints to aerospace parts. Swiss machining helps create tiny, highly-detailed components such as actuators, rotary shafts, and gas pins.
- Electronics: Swiss-turned components are very common in the electronics industry, helping to form and connect circuits. The process is ideal for electronic terminals and similar connective components.
- Medical and Dental: Swiss machining is ideal for creating tiny surgical pins and bone screws, as well as components for implants and medical devices.
- Military & Defense: Military aircraft, artillery, and missiles all demand high-performance, high-precision turned parts. Swiss turning is also the perfect choice for firearm nuts, pins, pistons, and barrels.
- Oilfield & Energy: Precision turning creates consistent and durable screws, nuts, spacers, and retainers ideal for the oil industry. Other applications include components used for monitoring pipelines and offshore rigs.
Swiss machining can benefit any industry that requires precision-turned components, especially when it’s important to maintain consistency across moderate-volume production runs.
Swiss Machining Capabilities
DACRUZ Manufacturing specializes in precision turning for individual components and sub-assemblies. At the core of our custom turning capabilities are Swiss machining centers, which enable accurate and consistent production runs at any volume. Our 30+ Star Swiss and Tsugami machines are each equipped with twin spindles and the live tooling capacity to perform multiple secondary processes. These include:
With these secondary capabilities, in many cases, we can produce net-shape components with just one cycle. For those components that require further secondary processing, our machining specialists perform additional operations in-house to ensure quality, efficiency, and cost-effective production.
Swiss Machining Capabilities
DACRUZ Manufacturing specializes in precision turning for individual components and sub-assemblies. At the core of our custom turning capabilities are Swiss machining centers, which enable accurate and consistent production runs at any volume. Our 30+ Star Swiss and Tsugami machines are each equipped with twin spindles and the live tooling capacity to perform multiple secondary processes. These include:
-
Slotting
Slotting is a cutting process used to create notches and grooves of varying depths and widths. It is a critical step in crafting many cylindrical components, including castle nuts and gear hubs.
-
Cross-Drilling
Cross-drilling creates holes through the middle of cylindrical components. It is typically used for components like valves and connectors.
-
Cross-Tapping
Our Swiss machines are capable of cross-tapping, or threading the inside of holes. Cross-taping on a Swiss machine speeds production of screws, nuts, and other threaded components.
-
Back Drilling
Back drilling, or controlled depth drilling, is a specific type of drilling that offers greater depth control and tolerance. It involves redrilling a hole using a slightly larger bit to remove excess material and ensure the depth is as exact as possible.
With these secondary capabilities, in many cases, we can produce net-shape components with just one cycle. For those components that require further secondary processing, our machining specialists perform additional operations in-house to ensure quality, efficiency, and cost-effective production.
Swiss CNC Machining at DACRUZ Manufacturing
OEMs seeking maximum quality, precision, and repeatability can benefit from the automated multitasking of Swiss CNC machining. At DACRUZ, we use Swiss machining for medium-to-high complexity parts in medium-to-high volume production runs. In these scenarios, Swiss machining offers the best repeatability and fastest turnarounds of any turning technique. To further optimize efficiency, we make use of continuous automated bar feeders to perform lights-out machining. In doing so, we are able to cut our short lead times even shorter by maximizing production hours.
Custom Turning Services at DACRUZ
DACRUZ is a trusted precision manufacturer servicing OEMs in the Northeast. We maintain strict compliance with ISO, TS, and FDA standards, and all of our products are backed by the most rigorous quality control procedures. Together, our advanced equipment, skilled professionals, and innovative methods allow us to adapt to any client’s needs.
To learn more about how Swiss machining improves our custom turning results, contact DACRUZ or request a quote today.